Challenges in High-Rise Building Design
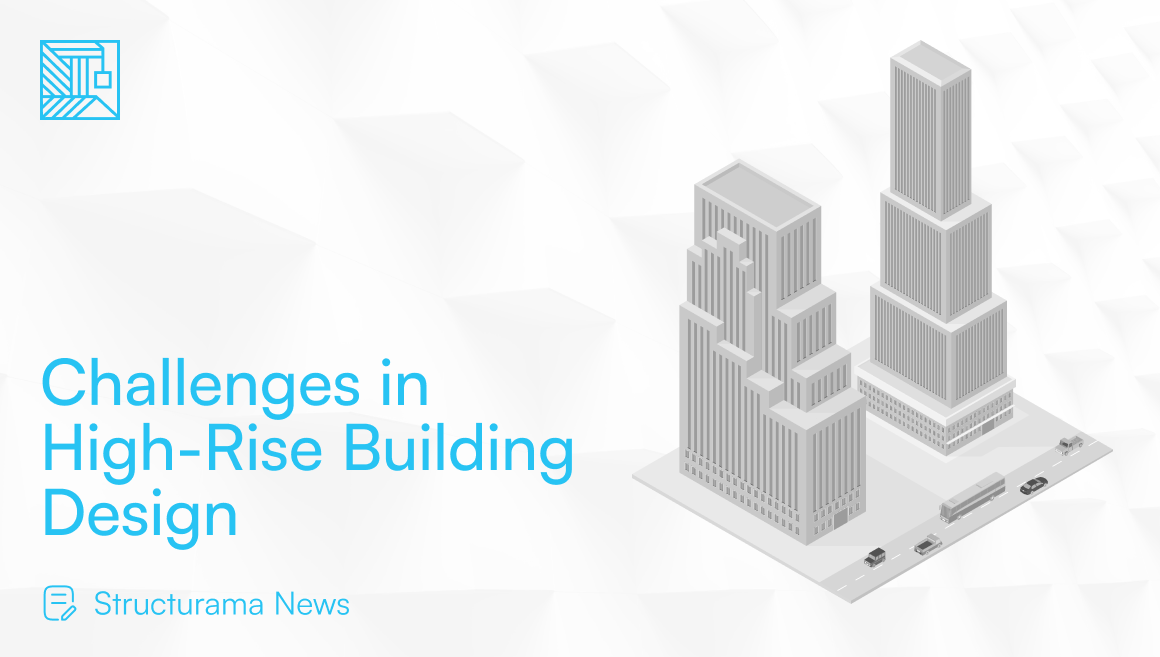
High-rise buildings have emerged as one of the trendiest signifiers of modern architecture as cities extend their territories with serious limitations of space in urban areas. These towering edifices are practically meant to answer the challenges brought about by urbanization, but high-rise building construction and design are not to be taken lightly. Meticulous planning and innovative technologies have an important role, as does an understanding of structural engineering that deals with safety, functions, and sustainability.
Managing huge loads, including advanced construction methods, makes high-rise construction unique — for demanding cases demand ingenious solutions. In this blog, we will survey high-rise building construction complexities, look into the construction processes making them realized, and discover how engineering innovations change the concept of vertical architecture. Whether you are interested in how are high rise buildings constructed or the problems engineers face in these types of projects, this guide will provide a narrowed, yet complete glance into one of the most exciting fields of modern construction.
What Qualifies as a High-Rise Building?
A high-rise construction is one that requires the vertical mechanical transportation of people and goods. Though there are regional differences in how they are described, in general, there seems to be an agreement that a high-rise building construction is at least 75 feet – roughly 23 meters high, with a minimum of around seven floors. In many cities, high rises are strong marks of vertical expansion and development as well as housing, business and mixed units.
But how does high-rise construction differ from other types of construction? The main difference is their height and use:
- Low-Rise Buildings: They contain no more than three floors. Elevators are not a necessity and basic accessibility is guaranteed. These are the default settings for suburban houses and smaller neighborhoods.
- Mid-Rise Buildings: Mid-rise structures range between four to six floors and tend to have elevators. They balance urban density and a more human scale of design.
- High-Rise Buildings: Anything exceeding seven stories falls into the high-rise category, often requiring advanced structural systems, mechanical systems, and fire safety measures due to the added complexity of vertical construction.
High-rise projects provide both new opportunities and construction challenges, hence they need to incorporate novel construction and design methods to match the surface and purpose of the model. These skyscrapers, designed for rental or large commercial areas, are the anchors of the cities of today and tomorrow and act as the drivers of urban appeal and modernization worldwide.
Construction Methods and Technologies for High-Rise Buildings
The modern engineering marvel of constructing high-rise buildings requires specialized methods and advanced technologies to ensure stability, safety, and efficiency. Both the materials and methods have been crafted to address unique construction challenges arising from such towering height structures. So, how are high-rise buildings constructed? Let’s find out more about the core construction methods and the advanced technologies that are popularizing these projects.
Core Construction Methods for High-Rise Buildings
Steel Frame Construction
Steel, with its superior strength-to-weight ratio, is one of the most commonly used materials for constructing high-rise structures. Steel frames form the skeleton of the building, efficiently bearing vertical loads while enabling the design of large, open spaces. This flexibility, combined with prefabrication options, makes steel construction an ideal choice for projects requiring short construction timelines.
Reinforced Concrete
Reinforced concrete is widely used in high-rise structures for its strength, fire resistance, and ability to withstand seismic forces. Concrete cores typically house elevators and stairwells, which are essential for providing lateral stability. This method is especially favored in regions where local material costs or expertise make concrete more economical than steel.
Composite Structures
Composite structures use steel and concrete together to exploit the advantages of each of them. Steel frames allow some flexibility, while concrete cores impart rigidity and stability, making this hybridization of steel and concrete most suitable for modern high-rise buildings. The right amalgamation of the strength of steel and the rigidity of concrete leads to better performance at a fair price in construction.
Construction Technology for High-Rise Buildings
Developments in construction technology have completely transformed the execution of high-rise projects, improving them in execution speed, precision, and sustainability.
Prefabrication and Modular Construction
Prefabrication, together with prefabricated construction, is the lifeblood of modern high-rise construction, thanks to extraordinary efficiency and accuracy. A significant amount of time and labor saved on-site can be realized by making building components off-site—such as facade panels, steel frames, and modular units. High-rise projects are the most suitable projects for this method because working at great heights poses particular logistics and safety difficulties.
For instance, prefabricated facade systems make the building’s outer shell enclosure process quicker, so the building interior work is not held up. Also, modular bathrooms or mechanical shafts can be made in one piece and easily lifted into place, thereby achieving easy installation and minimizing on-site interruptions.
Among the various benefits of prefabrication in tall buildings, the most important is the impressive quality control effect. In a factory setting that is well controlled, the components are produced to the required level of precision, which is often impossible to realize in an operating construction site. As a result, there are fewer expensive delays and a more reliable timeline.
These next few years are likely to witness changes with the introduction of modular designs and robotics that are going to be the blazed path of prefabrication in the high-rise construction industry. Due to the possibility of off-site creation, the next buildings would be taller and have more intricate components, suggesting that the modernization of skyscrapers will be marked with more safety along with creativity and speed.
Building Information Modeling (BIM)
BIM technology enables the creation of a detailed 3D model of the entire building, integrating architecture, structure, and MEP systems. With such digital approaches, it coordinates various stakeholders, minimizes mistakes, and makes construction a simpler process, especially for high-rise buildings having complex design structures.
Climbing Formwork Systems
Used extensively in reinforced concrete construction, climbing formwork systems allow for continuous vertical construction of core elements like elevator shafts. These systems improve efficiency by reducing the need to dismantle and reset formwork at each level.
High-rise construction is verily a product of human ingenuity, balancing older methods with newer cutting-edge technologies. Steel-frame skyscrapers or composite towers designed with BIM both hold qualitative bicriteria in precision, innovation, and resilience to create structures that change the face of our cities.
Construction Challenges in High-Rise Buildings
These tall buildings are engineered to face some specific issues that need creative solutions, accurate planning, and modern devices. From the huge challenge of structural and environmental integration, below are the top challenges in high-rise building construction and how modern tools like BIM tackle these issues.
1. Structural Stability and Load Management
Imposed vertical and lateral loads on high-rise buildings include the self-weight, weight of people, and external forces like wind and earthquakes. Structural engineers must make systems maintain stability without the additional burden of excessive material consumption or design rigidity. Some examples of such systems are reinforced concrete cores, steel frames, and composite structures.
2. Environmental Considerations and Sustainability
The increasing focus on sustainable construction brings a challenge to multistory mega projects to minimize environmental footprints. Energy efficiency, a reduction in CO2 emission, and sustainability in using materials are some of the main aspects to consider. Green building certifications require innovative designs, such as energy-efficient facades, solar panels, and rainwater harvesting systems, to make these towering structures more eco-friendly.
3. Fire Safety and Emergency Evacuation
The height of these structures results in complexities regarding fire safety and evacuation in emergencies. Designers must incorporate advanced fire suppression systems, fire-resistant materials, and pressurized stairwells. Additionally, creating safe and accessible evacuation routes for all occupants, including those with disabilities, is a critical aspect of the design process.
4. Wind Resistance and Earthquake-Proof Design
High-rise buildings are subjected to dynamic forces, which include wind pressure and seismic activity. A wind tunnel test is conducted to emit a building’s reaction to wind forces, while precautionary measures such as base isolators and tuned mass dampers are used on seismic-resistant designs to mitigate earthquake risks. These systems provide a stable structure and a safe environment for its occupants under extreme conditions.
5. Efficient Use of Space and Services
Integration and application of high-rise spaces concerning their mechanical, electrical, and plumbing (MEP) systems pose a great challenge to high-rise projects. The MEP systems should be efficient and space-saving, thereby opening more space for functional areas. All vertical transport systems, such as elevators and HVAC, must be planned judiciously across all floors without consuming too much energy or space.
How Modern Tools Help Overcome These Challenges
Building Information Modeling (BIM) plays a pivotal role in addressing these challenges. By creating detailed 3D models, BIM allows architects, engineers, and contractors to collaborate seamlessly, identify potential conflicts, and resolve issues before construction begins. For instance:
- BIM enables structural load analysis, helping engineers design systems that can handle both static and dynamic forces.
- Environmental performance simulations within BIM help optimize energy efficiency and sustainability.
- BIM models incorporate fire safety layouts, ensuring that evacuation routes and fire suppression systems are integrated into the design.
- The precision of BIM allows for efficient placement and coordination of MEP systems, reducing construction delays and material waste.
In parallel, prefabrication is transforming how these challenges are tackled, particularly in high-rise construction. By manufacturing key components off-site, prefabrication complements the precision of BIM. The integration of prefabrication into the BIM process ensures that all prefabricated elements are meticulously planned and fit into the overall design. For example:
- Prefabricated structural components designed using BIM can be manufactured to exact specifications, reducing errors during installation.
- Modular prefabrication speeds up construction timelines while maintaining high-quality standards.
- Factory production of facade elements ensures uniformity and minimizes the challenges of working at extreme heights.
Together, BIM and prefabrication represent a powerful combination that pushes the boundaries of urban development, creating safer, smarter, and more sustainable high-rise structures. By addressing these challenges with innovative tools and methods, high-rise building construction continues to evolve, achieving greater efficiency and precision.
Building the Cities of Tomorrow
High-rise buildings are a testament to human ingenuity, reshaping urban skylines and providing efficient solutions to the challenges of modern city living. However, their construction is not without obstacles, each phase demands meticulous planning and innovative solutions.
The introduction of modern construction techniques and technologies like prefabrication, modular systems, as well as BIM, has dramatically altered the nature of high-rise projects, allowing the entire construction industry to face certain construction challenges with greater effectiveness. Such innovations not only ensure the safety and functionality of high-rise structures but also contribute to a sustainable environment in urban landscapes.
At the end of the day, building the cities of tomorrow will combine a technologically skilled workforce with future-oriented design and a sustainability commitment. By embracing these principles, high-rise projects continue to meet the demands of growing urban populations while shaping cities that are both functional and inspiring.