Precast Concrete and Modular Construction: A Perfect Match
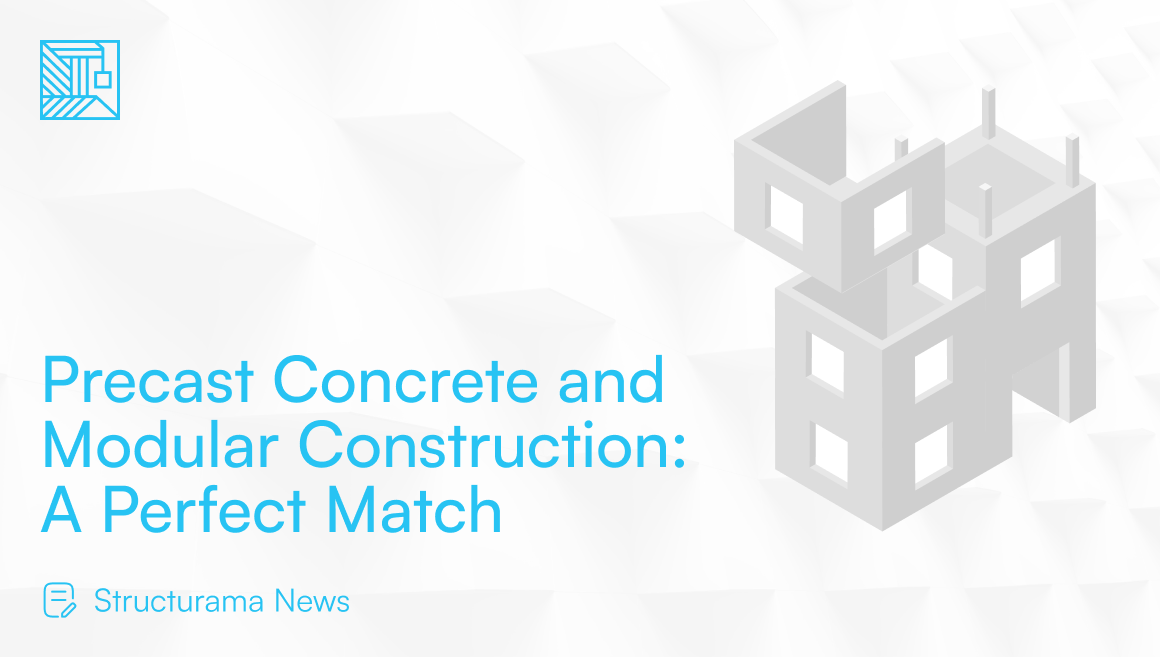
If someone were to ask you about your first association with modern construction, how likely is it that the notions that would come to your mind are speed, efficiency, and sustainability? As long as you are keeping up with the current demands of this industry – very likely.
Although traditional building methods are time-tested and trustworthy, they now struggle to meet the rapid demands and environmental considerations of projects. So, in the need to come up with an innovative approach that is both reliable and adept, precast concrete modular construction is coming to the spotlight.
This involves off-site fabrication of components in controlled settings, which are then transported to the construction site for assembly. Precast concrete modular construction expedites the completion of the projects while minimizing environmental disruptions and waste, being thus both timely and environmentally responsible.
What Is Precast Concrete Modular Construction – The Game-Changer in The Industry
By its definition, precast concrete is a construction material manufactured in a controlled factory environment before being transported to the site for assembly. By our definition, this is the material we get to thank for the higher quality, durability, and efficiency we’ve accomplished in the construction industry today. Unlike traditional cast-in-place concrete, poured and cured on-site, precast elements are fabricated under precise conditions, reducing on-site labor and speeding up project timelines significantly.
However modern an invention it might be, its beginnings can be traced back to ancient Rome, where early forms of prefabricated stone blocks were used in construction. The modern precast industry as we now know it took shape in the early 20th century, transforming building techniques with advancements in reinforced concrete and industrialized production. From the current standpoint, it’s almost certain that precast concrete technology will evolve even further through the integration of smart materials, automation, and sustainable innovations.
What Is Modular Construction – A Smarter Way of Building
Modular construction got its name by being a building method that involves assembling prefabricated modules before transporting them to the site for final installation. These modules are structural units manufactured in a controlled environment. Two main types of modular construction are:
- Permanent Modular Construction (PMC) – PMC structures are designed for long-term use; they easily integrate with conventional buildings and often use precast concrete for added durability.
- Relocatable Modular Construction (RMC) – RMC units are prefabricated and can be disassembled, moved, and reused for temporary applications like emergency shelters or even schools and offices.
Precast concrete systems are not separable from the modular construction narrative – they play a key role in structural strength, fire resistance, and energy efficiency. The combination of these technologies creates high-performance, precast concrete modular buildings that meet all of the modern demands.
Types of Precast Concrete Systems
1. Structural Precast Components
Structural precast elements yield the core framework of buildings and infrastructure. These include precast beams, columns, load-bearing walls, and floor slabs, which enhance structural stability, load distribution, and construction speed. Precast concrete frames are widely used in high-rise buildings, parking structures, and large industrial projects because of their strength and efficiency.
2. Architectural Precast Components
Precast concrete is mostly important due to its strength – but that is not even the only benefit. It also plays an important role in architectural design. Facade panels and decorative elements allow for customized textures, patterns, and finishes, improving aesthetic appeal and thermal performance. Precast cladding allows for weather resistance, durability, and insulation benefits, making it a preferred choice for exterior walls.
3. Precast Foundations
Precast foundations, such as footings and pile caps, provide a consistent, high-quality alternative to traditional foundation work. Manufactured in a controlled environment, these elements ensure uniform strength, reduce on-site labor, and allow for faster installation, which is particularly beneficial in projects with tight timelines.
4. Precast Bridge & Infrastructure Components
Large-scale infrastructure projects rely on precast concrete for strength, longevity, and efficiency. Common applications include precast girders, bridge decks, tunnel segments, and highway barriers. These components allow for rapid assembly, reduced traffic disruptions, and increased durability, making them an essential part of modern transportation networks.
Types of Modular Construction
There are various forms of modular construction, each of them offering some unique advantages in terms of speed, flexibility, and overall efficiency.
1. Volumetric Modules
Volumetric modular construction involves the off-site fabrication of fully enclosed three-dimensional units, which are then transported and assembled on-site. These modules include walls, floors, ceilings, and even pre-installed fixtures. They are ideal for apartments, hotels, hospitals, and office buildings, where repeatable designs and fast deployment are priorities.
2. Panelized Systems
In this method, prefabricated wall panels, floor slabs, and roof sections are produced off-site and then assembled on location. Unlike volumetric modules, panelized systems require on-site assembly but still reduce overall construction time. These are widely used in residential housing, commercial structures, and low-rise buildings due to their cost-effectiveness and ease of transportation.
3. Hybrid Modular Construction
Hybrid modular construction combines both volumetric and panelized elements, optimizing speed, design flexibility, and structural efficiency. This method allows critical structural components to be prefabricated while leaving room for customization on-site. We see it as providing the best of both worlds – enabling high precision, architectural adaptability, and streamlined assembly for complex building projects.
Key Benefits of Modular Precast Systems
Let’s go over the main benefits that put precast concrete modular construction above traditional methods:
1. Faster Construction Time
One of the most significant advantages is the ability to manufacture components off-site while site preparation occurs at the same time. This parallel workflow drastically reduces project timelines and minimizes weather-related delays, leading to faster project completion.
2. Cost-Effectiveness
The usage of modular precast concrete reduces labor and material waste during the project lifecycle. As factory conditions are completely controlled, errors are also highly reduced.
3. Sustainability & Environmental Impact
Efficient material usage in these methods leads to reduced carbon footprint and energy-efficient buildings with improved insulation.
4. Structural Strength & Durability
Precast stands for high-performance concrete with enhanced longevity. It stands out in its resistance to fire, seismic activity, and harsh weather conditions.
5. Improved Safety & Quality Control
Factory-based production minimizes on-site risks, which are more often than not present in traditional construction. Moreover, higher precision in manufacturing ensures consistency in quality.
Challenges & Limitations
The biggest challenge arises when it comes to transportation and logistics due to the, to say the least, large size of components. This calls for high initial investments in manufacturing facilities.
Furthermore, design flexibility may be limited compared to traditional construction since standardization is often a must. Last but not least, the industry’s skepticism towards these newer methods can hinder widespread adoption.
Applications of Precast Concrete Modular Buildings
Precast and modular construction are widely applied in residential buildings, commercial and office spaces, healthcare facilities and hospitals, as well as educational institutions and student housing. Finally, infrastructure projects such as bridges, tunnels, and railway stations leverage precast components for improved durability and faster construction.
Future Trends in Precast Concrete Modular Construction
We expect the future of precast and modular construction to be shaped by cutting-edge technologies, creating a construction reality where integration of AI and BIM will enable more enhanced design and planning, 3D printing will change possibilities when it comes to shapes and needed times of precast concrete components, and green building innovations will drive sustainability efforts.
Smart precast panels equipped with IoT sensors are expected to enable real-time monitoring of building conditions for improved maintenance. As unbelievable as it until recently may have sounded, the construction industry is moving towards fully automated construction sites with increased work speed and reduced human error.
To Conclude
It is undeniable that precast and modular construction offer benefits in terms of speed, cost-efficiency, sustainability, and structural durability. These methods address the biggest modern challenges when it comes to construction, among them labor shortages, environmental impact, and the need for speed.
Embracing innovative solutions will lead us all toward smarter and more resilient building processes.