Precast Concrete Methods for Bridges, Tunnels, and Modern Infrastructure
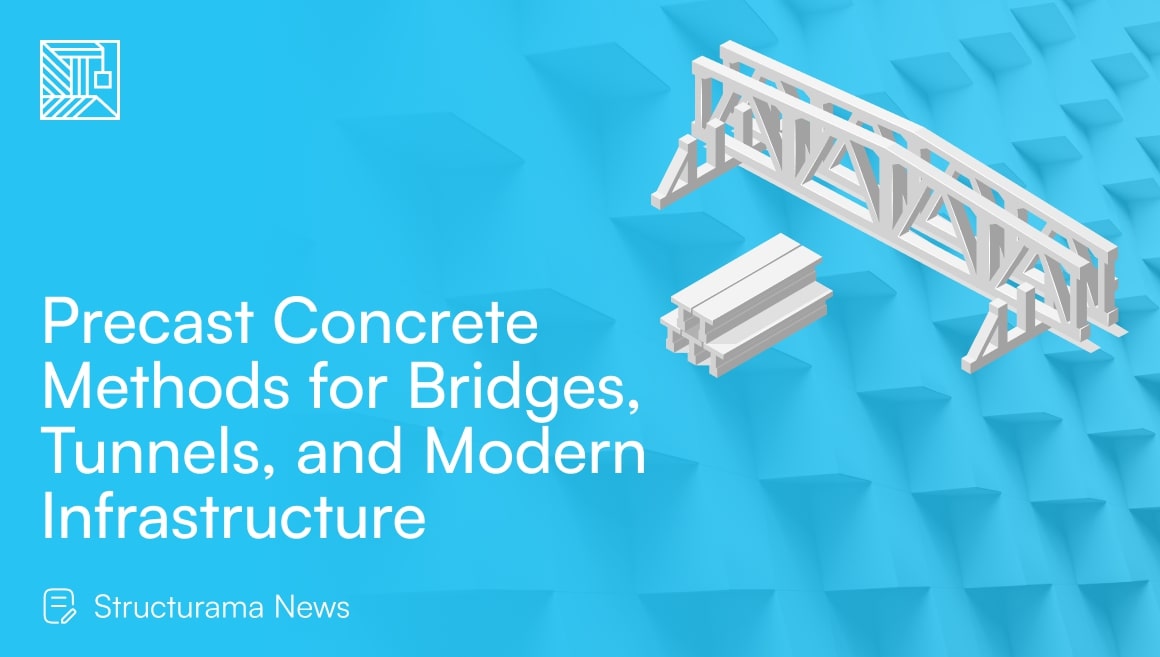
Whether your client is a city government or real estate developer, durable and quickly deployable solutions are a priority. Yet, unfavorable weather conditions can delay development, more so when working with cast-in-place concrete construction.
Other factors, like material consistency or workforce safety risks, also affect the timeline and success of your project. Instead of reacting to these challenges, anticipate and solve them with precast concrete methods.
Precast construction starts off-site, manufacturing components such as bridge girders, tunnel linings, and deck panels, and you then assemble them on-site. Producing these ready-made elements requires methods like panel systems, beam-and-slab configurations, and segmental construction, which improve precision and reduce on-site labor.
With precast methods, you sidestep weather delays, minimize risks, and guarantee consistency—allowing you to build confidently from day one.
Precast Concrete Methods for Bridges
Precast concrete doesn’t just save money: up to 38% for single-story buildings and 32% for two-story ones; it also speeds up construction for projects like bridges, slashing labor costs and minimizing weather delays.
Key Applications in Bridge Construction
- Precast bridge girders: Precast girders support maximum efficiency in bridge construction through large structural components built off-site and installed quickly. Since they’re molded in a factory, they offer consistent quality and strength while reducing the time crews spend on-site. Many reasons pushed precast concrete bridges to the forefront of reliable choices for modern infrastructure, but the speed and minimal traffic disruptions typically come first.
- Deck panels and abutments: In the precast method of bridge construction, specialized companies make deck panels and abutments off-site, while bridge construction crews assemble them on location, cutting down build time without sacrificing quality. Precast deck panels are shortcuts to quicker installation without waiting for concrete to cure, while precast abutments provide a solid, uniform foundation.
- Barriers and parapets: The precast bridge construction method makes installing barriers and parapets noticeably faster while ramping up efficiency. Precast barriers are a must-have protection for traffic, and parapets are there to ensure safety and structural support.
Advantages in Bridge Projects
- Reduced construction time with off-site prefabrication: All precast concrete components come from settings with controlled parameters without disrupting site work. With parts ready to assemble as soon as they arrive, projects can move forward without waiting for on-site curing, so you don’t have to think about whether you’ll have to extend the project timeline or face weather-related delays.
- High precision and quality control in manufacturing: The precast method of bridge construction promotes greater accuracy and quality control by manufacturing components in factories with strict standards. It follows consistent processes and rigorous quality checks to guarantee that each element meets exact specifications.
- Durability for long-span and load-bearing structures: Exceptional durability is often the first characteristic that comes to mind when using the precast method of bridge construction for long-span and load-bearing structures. Why? Precast concrete elements have no difficulty withstanding harsh weather, wear, and environmental factors, making them well-suited for high-stress applications like bridges.
Precast Concrete Methods for Tunnels
Precast concrete bridges aren’t the only possibility for lasting infrastructure. Here’s how this method fares in terms of tunnels.
Applications for Tunnel Construction
- Tunnel lining segments: Fast and reliable underground construction should be an unquestionable expectation without disrupting on-site development or dealing with unexpected issues. You can halve excavation time and simplify assembly as all your team has to do is install these segments, easing up on labor demands. Precast concrete tunnel solutions are the obvious choice when building metro systems and road tunnels because they’ll support structural integrity, all while resisting water infiltration and ground pressure.
- Ventilation and drainage components: Precast concrete shapes everything from underground culverts to custom air ducts and allows this infrastructure to run smoothly without long construction delays. These components push back excess water from roads and foundations while still managing airflow in tunnels, parking garages, and industrial spaces.
- Shafts and entry portals: The precast construction method makes excavation and assembly rather predictable and exceptionally fast due to tight tolerances. Whether it’s for tunnels, mines, or underground utilities, these structures must handle intense loads while resisting water and soil pressure, and that’s what you need the precast segments for.
However, you should consider the following technical requirements:
- Precision manufacturing for tight tolerances: Even the slightest deviation in measurements can result in assembly misalignments, potentially costing extra bucks and dragging the timeline. The good news is that you can prevent this if you go for components manufactured with tight tolerances, often within millimeters. If you’re working in bridge construction, beams must fit perfectly with bearings to prevent structural stress and long-term damage.
- Resistance to high-pressure loads and environmental factors: Precast concrete has to withstand immense pressure and harsh environmental conditions, so its composition, reinforcement, and curing process matter as much as every other detail. For example, bridge segments face constant vehicle loads and exposure to moisture, so crews must work with dense mixes and corrosion-resistant steel.
Advantages in Tunnel Projects
The following reasons should be enough to introduce the precast concrete tunnel solutions into your projects:
- Accelerated construction timelines: Rest assured your projects won’t suffer delays with precast concrete methods, as there’s no need for traditional pouring and hardening. They also offer greater structural accuracy, which is why cities like London and Tokyo use precast tunnel linings to handle extreme pressure and moisture while reducing long-term maintenance.
- Higher safety during installation: Precise, pre-manufactured tunnel segments that fit together with zero to no adjustments are among the main reasons companies choose the precast concrete method. The best part is that their installation requires fewer workers to perform risky tasks underground, meaning fewer accidents and injuries during construction.
- Customization for curved or complex geometries: Although you can order customization for traditional cast-in-place concrete, the precast concrete method has an edge. These solutions allow for the pre-manufacturing of tailored pieces off-site, which are then brought to the site ready for installation.
Precast Concrete in Modern Infrastructure
You can use precast concrete methods beyond just building bridges and tunnels.
Urban Infrastructure
You can build smarter and more durable city spaces with precast concrete methods that deliver pieces ready for installation. Moreover, you can cut down on construction time and quickly set up sidewalks, curbs, and drainage systems.
Rail Infrastructure
Precast concrete works well for durable sleepers that withstand constant pressure, as well as platform sections that speed up construction. But you can also assemble retaining walls in no time without sacrificing strength or stability.
Roadways
When it comes to roadways, precast concrete can simplify building noise barriers, culverts, and embankments, as it has all it takes to keep projects moving fast with minimal surprises.
Ports and Harbors
In ports and harbors, sea walls and dock structures made with precast concrete units come together quickly, resisting the tough conditions of saltwater and weather.
What About the Future Trends in the Precast Concrete Method?
Precast concrete has the potential to make wind turbine foundations more efficient, as it can trim down on material use and accelerate installation. Companies using precast post-tensioned segments can, for example, lower the amount of concrete while still providing the strength necessary for these massive structures.
Precast concrete is on the way to becoming a key player in smart city projects as the pathway to sustainable and flexible solutions for creating energy-efficient buildings. Thanks to its versatility, designs don’t have to separate modern technology from eco-friendly materials.
Some of the best examples are the Mashhad CEO Headquarters in Iran, which brings traditional and contemporary architectural styles together, and India’s Cybertecture Egg, which showcases how precast concrete can promote smart features like green spaces and energy-efficient technologies.
Innovative Precast Concrete Methods
- Use of Building Information Modeling (BIM) in precast design and planning: BIM has revolutionized the development stage of precast concrete, moving away from basic 2D drawings to detailed 3D models you can share and update in real-time. You can streamline the entire building process with this tech so that each precast element is accurately modeled with all necessary details like structural specs and reinforcements.
- 3D concrete printing and prefabrication: Thanks to 3D printing, custom, detailed pieces are no longer out of your reach, as production speeds up dramatically. Meanwhile, you can use prefabrication to build entire project sections off-site, including bridges and walls.
- Embedded sensors for structural health monitoring: The principal perk of this tech is that you can continuously track the condition of bridges and buildings. Wear and tear cease to be a major threat as you can detect signs early on and foster proactive maintenance.
Sustainability in Precast Methods
- Reduction of waste during manufacturing: Precast concrete is molded in a well-organized factory, translating into precise measurements and efficient molds that slash scrap material and excess production.
- Use of eco-friendly materials and recycled aggregates: One of many positives of precast methods is the continuous effort to give new life to materials that would otherwise end up in landfill.
- Energy-efficient production processes: The precast concrete method requires companies to manufacture components off-site, making it an inherently more sustainable construction choice.
What is the Downside of Precast Concrete?
- Transportation of large precast elements: Although transporting oversized pieces may sound tricky, careful planning is the key: specialized transport vehicles and timing coordination should help you bypass traffic and delays.
- Addressing design limitations for complex projects: The pre-made components in precast concrete can be limiting, but the goal is to keep your engineers and designers in the loop. They can customize size, shape, or connection points to fit the project or even combine different precast components.
Conclusion
Skyrocketing costs and unexpected delays are often pressing issues in construction. Precast concrete relieves you of this worry, as it streamlines the development while making room for versatility and continuous advancements.
As a method that involves manufacturing components off-site, it’s more efficient and sustainable than traditional options without pushing quality aside. Since your infrastructure needs deserve only the best standards, consider adopting the precast concrete method and making success the only outcome.