Quality Control in Precast Concrete Production
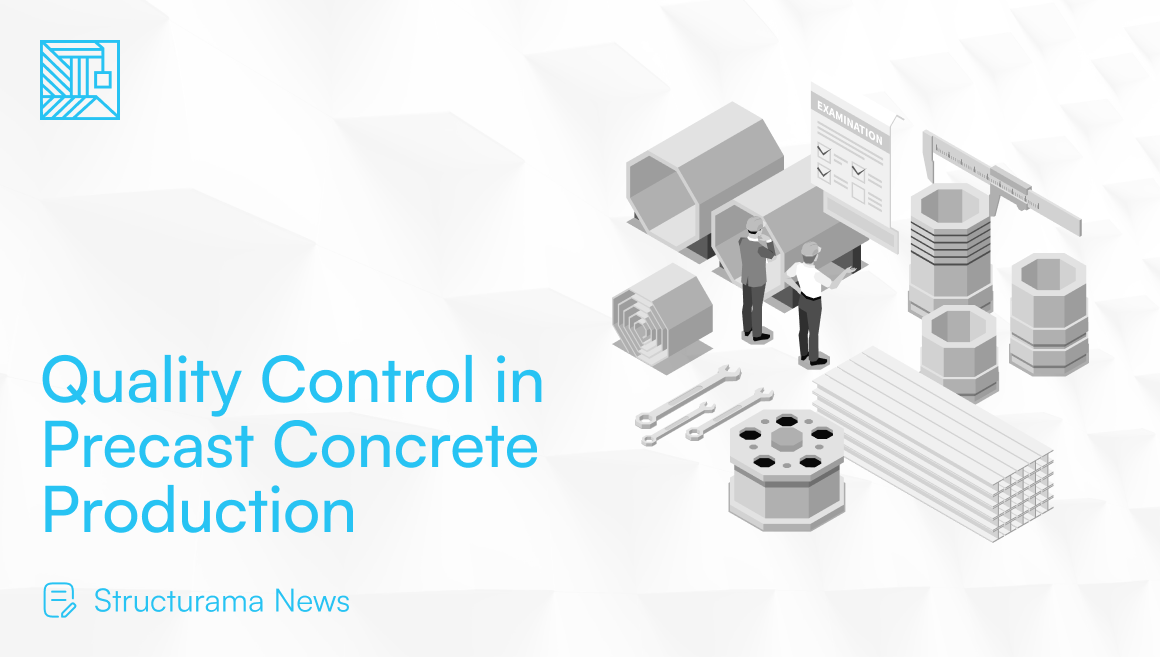
The wide usage of precast concrete in construction speaks for itself – this material transformed and is still transforming the construction industry as a whole. Let’s rewind for a brief moment to remember that precast concrete is made by casting concrete into reusable molds, curing it off-site, and then transporting it for installation, saving thus a lot of time and resources. The applications of PC range from structural components like slabs and beams to decorative elements in buildings.
As it is often an integral part of the building structure, it is vital to ensure high quality in its production, so as to maintain safety and integrity in construction projects. This is where precast concrete quality control comes into the picture as its frame – since there is no exhibiting of precast projects without precast quality control.
What Is Precast Concrete Quality Control?
Quality control in precast concrete construction refers to a systematic approach to monitoring and maintaining the quality of concrete components produced in a controlled environment. This means following the prescribed condition rules to ensure the structural integrity, durability, and performance of precast elements meet industry standards.
The role of quality control is not additional but critical, it exists as a concept to prevent any defects or safety risks by adhering to strict regulations and fulfilling customer requirements. Especially when it comes to construction projects, delivering components that comply with design specifications and regulatory frameworks is beyond essential.
Key Components of Precast Concrete Quality Control
Quality-controlled concrete involves monitoring at each stage of precast production, be it material selections at the very beginning or final testing at the very end – the components must meet design and regulatory standards.
1. Material Selection and Testing
The quality of raw materials, including cement, aggregates, and admixtures, directly impacts the durability of precast elements. Aggregates, for instance, must conform to the size and cleanliness specifications in order to avoid inconsistencies.
2. Mix Design
Proportions are fine-tuned through trial mixes to achieve optimal strength and workability, adjusting for environmental factors like temperature.
3. Production Monitoring
Trained personnel oversee mold preparation, batching, mixing, and curing. Molds, for instance, must be checked for accurate, within millimeters precise dimensions, ensuring thus compatibility during installation.
4. Dimensional Accuracy and Surface Finish
Inspection techniques serve here to prevent surface defects like cracks or voids, making sure the finished product meets aesthetic, and, above all, structural requirements.
5. Final Testing
All precast components undergo load testing and other evaluations to confirm durability, with test results documented to meet compliance and traceability standards.
Precast Concrete Quality Control Checklist
Let’s go over the most important steps that must be checked when it comes to quality control in precast concrete construction.
1. Material Certification and Equipment Inspection Before Production
Before production begins, the first step is to verify the certifications of all raw materials. This means aggregates, cement, and admixtures all have to meet the required standards. Molds and equipment inspection is just as critical, with tolerances within ±1-3 mm for accurate dimensions and functionality. The mix design must be approved as well based on project specifications and trial results, ensuring it aligns with the concrete’s intended strength and durability.
2. Proper Conditions During Production
During the production itself, batching and mixing processes must be supervised to maintain consistency in the mix ratio. It is also important to verify the concrete is properly placed, compacted, and uniform. Curing conditions must be carefully controlled, with temperatures maintained around 20°C and humidity levels kept in check to ensure optimal hydration.
3. Final Testing After Production
After production, the most important step is the thorough inspection for dimensional accuracy and surface defects, confirming they meet the required design tolerances. The surface flatness requirement is ±3mm. Strength tests, such as compressive strength evaluation, must be conducted, alongside durability assessments to ensure the concrete will stand the test of time. Last, but not least, all results must be documented, with any discrepancies addressed to maintain compliance with quality standards.
Benefits of Effective Precast Concrete Quality Control
Needless to say, quality control can only have benefits, but in the precast narrative, the benefits are unmissable.
Enhanced Product Reliability
Effective precast quality control makes sure that products consistently meet required strength and durability standards. This minimizes the risk of structural failures and ensures therefore long-term performance and safety in construction projects.
Cost Savings
Maintaining strict quality control reduces waste, which then minimizes the need for reworks. All of this translates to lower material costs and decreased likelihood of expensive repairs and costly maintenance long-term.
Improved Customer Satisfaction
Producing high-quality precast solutions consistently means meeting, and often even exceeding the expectations of the clients. And we all know consistency in meeting expectations is what it takes to build a strong reputation as a reliable and trustworthy partner.
Compliance with Standards
Adherence to both local and international construction codes leads to legal compliance of precast concrete products, which should be a non-negotiable. Prevention of legal and regulatory issues safeguards both the manufacturer and the client.
Challenges in Precast Concrete Quality Control
It never is all smooth and easy, and precast quality control comes with a set of challenges worth overcoming.
Variability in Raw Materials
Raw materials, such as aggregates and cement, often exhibit inconsistencies in quality and composition, which can impact the overall strength and durability of precast concrete.
It is crucial to establish a strict sourcing process, perform regular testing of aggregates and cement, and use admixtures to optimize the mix. Maintaining strong supplier relationships and implementing rigorous quality assurance protocols during material handling and storage can also help minimize inconsistencies and ensure more predictable results in precast concrete production.
Environmental Factors Affecting Curing and Production
Temperature fluctuations, humidity, and other environmental conditions can hinder the curing process, leading to variations in concrete strength and performance.
Monitoring and adjusting the production environment as needed, particularly during extreme weather conditions, can ensure the concrete cures evenly and reaches its full strength potential, ultimately improving the quality and consistency of the precast products.
Ensuring Workforce Adherence to Procedures
Consistency in production processes relies heavily on workforce discipline and adherence to detailed quality control procedures.
Provide regular training, clear communication of procedures, and consistent monitoring of operations. Encourage a culture of accountability and reward adherence to quality standards to motivate workers to follow best practices. Supervisors and quality control experts on-site should offer guidance and ensure compliance throughout the production process.
Keeping Up with Evolving Standards and Technologies
As construction codes and manufacturing technologies evolve, it becomes a must to continuously update practices to stay compliant and competitive.
Best Practices for Quality Control in Precast Concrete Production
As mentioned above, regular training and certification for production teams should be indispensable when it comes to the construction industry generally, as should investing in modern equipment and technologies. What additionally helps QC in precast is the implementation of a robust quality management system (QMS), and of course, continuous and never-ending improvement through feedback and audits.
Responsible for Excellence in Precast Concrete: The Role of Quality Control
There is no guarantee of safety, durability, or success in construction projects without effective quality control. A consistent focus on it does more than ensure compliance with standards – it builds customer trust and company reliability.
Read More:
The Environmental Benefits of Using Precast Concrete
The Role of Precast Concrete in Disaster-Resilient Buildings
Cost-Effectiveness of Precast Concrete in Large-Scale Projects